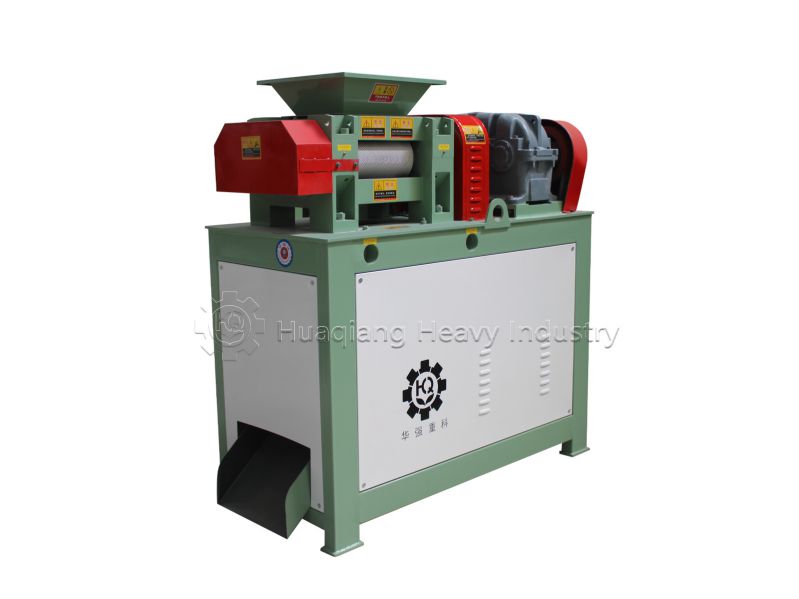
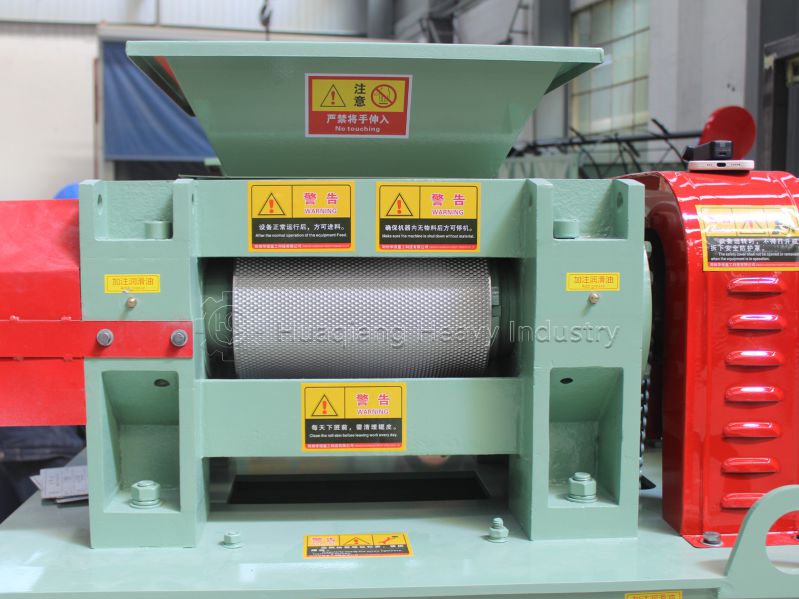
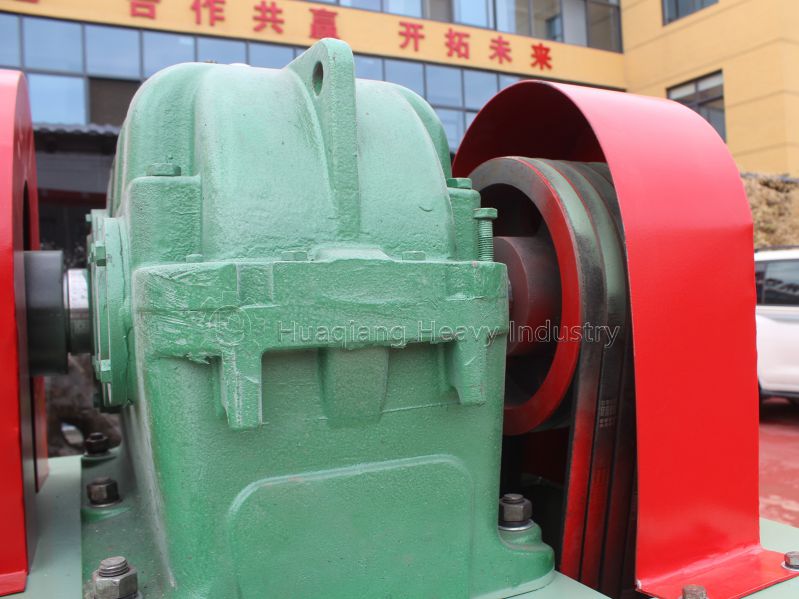
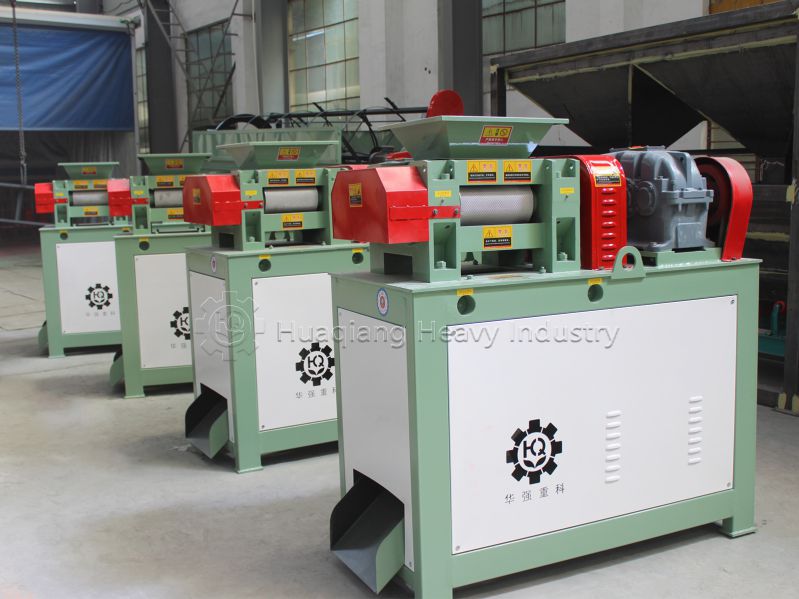
Double Roller Press Granulator
Double roller press granulator is an efficient and environmentally friendly granulation equipment widely used in industries such as fertilizers, chemicals, pharmaceuticals, food, and environmental protection. Its main function is to form particles with certain strength and shape by high-pressure extrusion of powdered or small granular materials, in order to improve the flowability and usability of the materials, and also facilitate packaging, transportation, and storage.
Scope Of Application
The roller extrusion granulator is suitable for granulating various materials, including but not limited to:
Fertilizer industry: organic fertilizers, compound fertilizers, slow-release fertilizers, etc.
Chemical industry: catalysts, dyes, pigments, plastics, rubber additives, etc.
Pharmaceutical industry: pills, intermediates of pills.
Food industry: seasoning, food additives, feed, etc.
Environmental protection industry: sludge treatment, coal slurry shaping, waste resource utilization, etc.
Equipment Structure And Composition
Feeding system: including feeding hopper and material conveying device, used to evenly feed materials between the pressure rollers.
Roller component: a pair of adjustable rotating rollers that are the core components of the granulation process. By adjusting the gap and pressure between the rollers, the granulation effect is controlled.
Crushing system: used to break the extruded sheet into small pieces.
Screening system: used to screen out qualified particles and remove particles that are too large or too small.
Control system: including drive device, speed control device, and pressure control system, used for precise control of the operating status of equipment.
Cooling system: used to cool the material after granulation to stabilize the particle structure.
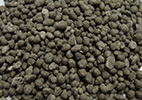

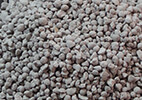
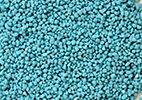
Working Principle
Material preparation: Before entering the roller, the material usually needs to undergo pre-treatment, such as crushing, mixing, and appropriate humidification, to improve its plasticity and flowability for subsequent extrusion granulation.
Material feeding: The pre treated material is evenly fed between two rotating pressure rollers through a feeding device. The design of the feeding device ensures the continuous and uniform distribution of materials to maintain the stability of the granulation process.
High pressure squeezing: When the material enters the narrow gap between two rotating pressure rollers, it is subjected to high-pressure squeezing. The rotation direction of the roller is usually opposite, which helps the material to be compacted and pushed forward under pressure.
Material deformation and forming: Under high pressure, the gaps between particles of the material decrease, and the material is compacted to form a sheet-like or strip-shaped structure with a certain thickness. This process relies on the plastic deformation of the material, allowing it to maintain a certain shape under high pressure without immediately collapsing.
Fragmentation and particle formation of sheet-like materials: The extruded sheet-like or strip-shaped materials are then sent to a crushing device, such as a crushing drum or cutting blade, to crush the sheet-like materials into small pieces. These small pieces are naturally or further broken into particles of the desired size through mechanical force during subsequent screening and cooling processes.
Particle cooling and screening: The formed particles may need to be cooled to stabilize their structure, and then unqualified particles are removed through screening to ensure uniform particle size in the final product.
Equipment Features
High pressure molding: Through high-pressure extrusion, materials that are difficult to cure can be effectively molded, resulting in good molding effects.
Wide applicability: Strong adaptability to materials, able to handle various properties of powdered or small particle materials.
Particle uniformity: By precisely controlling the pressure and roller gap, particles with regular shapes and uniform sizes can be produced.
Continuous production: capable of achieving continuous material feed and particle output, with high production efficiency.
Low energy consumption: Compared to other granulation methods, the energy consumption of the roller extrusion granulator is relatively low.
Compact structure: The device has a relatively simple structure, occupies a small area, and is easy to maintain and operate.
Environmental protection and energy conservation: The granulation process produces less dust and low noise, meeting environmental requirements.
Have Any Problem? Please, Contact
Integrity
Adhere to honesty and trustworthiness, be responsible to customers, employees, partners, and society, and establish long-term trust relationships.
Win win
Establish win-win relationships with all stakeholders such as customers, suppliers, and employees to share the fruits of enterprise development.